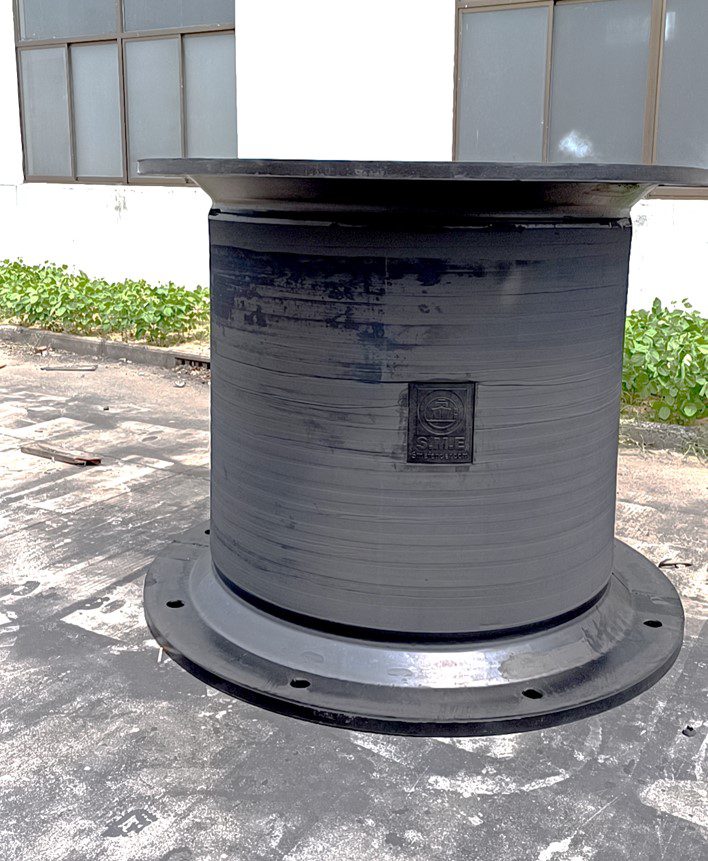
Engineered Fender Systems and Bollards
for Ports, STS Transfers, and Marine Infrastructure.
SME Fender Systems are excellent protection systems that have been tested and proven in long-term practice. They are the result of SME’s nearly 20 years of rubber technology accumulation and rich practical experiences in offshore engineering. Their excellent performance and superior durability have been recognized by customers worldwide.
Shield Marine Equipment (SME), established in 2005, is a global leader in the manufacturing of rubber fenders and mooring bollards. With extensive expertise in rubber and casting technologies, combined with deep practical experience in marine engineering, we focus on enhancing the performance and durability of marine fender systems and mooring bollards through innovative design, leading and raising the safety standards for marine docking and mooring operations.
We specialize in providing custom engineering solutions tailored to meet the unique requirements of each project. Renowned for our superior quality, we employ advanced manufacturing processes and rigorous testing to ensure the highest standards.
Our products incorporate the latest rubber formulations and casting technology, ensuring reliability under heavy loads and shear forces.
Our product range includes fixed fenders, floating fenders, marine airbags, marine bollards, quick release hooks, and marine steel structures.
Our fender systems utilize the original RMD rubber formulas. The advanced manufacturing processes and product structures effectively improve the anti-fatigue and anti-shear abilities of the fender bodies, which greatly increase the service lives of the fenders. They reduce the failure rates and ensure reliability in emergency situations.
Mechanical property inspection of rubber fenders is an important part of ensuring their quality and performance. Through strict test process and data analysis, the qualification of rubber fenders can be comprehensively evaluated, providing a reliable basis for actual delivery.
Compression test:
Compress the rubber fender to 10%, 20%, 30% of its standard height at a set speed until the designed compression deformation is reached.
Each time the compression reaches the predetermined percentage, record the corresponding pressure value.
After an interval of 30 minutes, repeat the above compression process twice to obtain stable data.
Take the average value of the last two compression data and draw a reaction force deformation curve.
Mooring bollards represent a harmonious blend of traditional craftsmanship and modern technology, utilizing high-strength materials, exquisite casting techniques, meticulous polishing, and internationally certified painting and corrosion protection, all of which ensure consistency in quality from the inside out, guaranteeing durability and longevity.
SME team, leveraging our expertise in engineering and materials science, customizes the design, manufacture, and testing of specific bollards in accordance with BS 6349 Part 2: 1998 and PIANC 2002 standards. We ensure that each bollard exceeds our clients’ expectations.
Every bollard is assigned a unique identification code, enabling us to trace back to the very first stage of production and access its comprehensive records.
Each technical submission file includes detailed FEA (Finite Element Analysis) and calculations, providing comprehensive support and transparency to our clients.
Our laboratory conducts simulations to test the capability of mooring bollards under 1.5 times the normal load force at various angles, in order to comprehensively evaluate their load-bearing performance and safety.
With a comprehensive range of molds and advanced production equipment, we possess superior rapid delivery capabilities, ensuring that our products are delivered to customers on time, accurately, and with superior quality.
Planning to purchase or upgrade your port fender systems and bollards?
TEL: +86 25 7811 2581
PH: +86 135 1251 3351
Email: smefender@gmail.com
Expert in
Fender system &
Bollard solutions
© 2024 Shield Marine Equipment Ltd. All Rights Reserved